 |
您目前的位置:首页--改造讯息 |
|
编者按:瓦斯是令人谈之色变的煤矿杀手,其实,瓦斯还有另一个名称——煤层气,主要成分为甲烷,是一种洁净优质的能源和化工原料。目前国内煤层气大量放空,利用率仅为28.7%。4月12日,国内首套低浓度煤层气深冷液化工业化试验装置在松藻煤电公司逢春煤矿建成,为煤层气变废为宝利用描绘了光明的前景。
4月12日,由中国煤炭科工集团重庆研究院、重庆能源集团松藻煤电公司、中国科学院理化技术研究所三家单位共同建设的国内首套低浓度煤层气深冷液化工业化试验装置在松藻煤电公司逢春煤矿建成,该装置采用国际先进的MRC混合制冷工艺(深冷精馏法),在-182度的低温和0.3mp的低压下同步进行含氧煤层气的分离和液化,每天能处理甲烷含量为29%—31%的低浓度煤层气(瓦斯)4800立方米,生产液化甲烷气(LNG)1.1吨。煤层气液化提纯后,其体积缩小为原来的1/625,甲烷浓度达到99%以上,达到工业和民用使用标准。
采访中多位专家向记者表示,煤层气是一种具有强烈温室效应的气体,如果直接排放到大气中,它的温室效应要比二氧化碳大20倍。同时,煤层气又是一种清洁能源,燃烧时不会产生烟尘和二氧化硫气体。我国的煤层气资源极为丰富,储量居世界第一位,约为美国的三倍。由于安全、技术等方面的原因,我国《煤矿安全规程》规定甲烷浓度低于30%的煤层气不能直接利用,致使我国煤层气开发利用较少,每年排入大气的煤层气占全世界采煤排放的煤层气总量的三分之一。甲烷浓度低,煤层气浓缩在安全性、技术、经济等方面还不够理想等原因阻碍了煤层气的大规模利用。“现在煤层气的利用率不到30%,如果能将低浓度煤层气也利用起来,不仅有效利用能源、节能减排,还能减少瓦斯给煤矿安全带来的危害,提高安全生产水平。”一位专家告诉记者。
“低浓度煤层气深冷技术提纯工艺及装备研究”是“十一五”国家科技重大专项“大型油气田及煤层气开发”的一个子项目,由中国煤炭科工集团重庆研究院承担。该项目负责人重庆研究院副总工程师王长元告诉《中国能源报》记者,该装置于4月6日上午10时系统投料运行,当晚19点50分生产出LNG。经过系统的操作调整,于7日中午12时达到设计指标,LNG甲烷浓度99.10%,回收率98.75%,综合电耗为2.8kwh/m3,LNG产量1.1t/d。
首创低浓度瓦斯开发技术
瓦斯开采利用是一个世界性难题。美国于20世纪70年代后期和80年代进入煤层气勘探开发的黄金时代,此后,英国、德国、澳大利亚等国也积极加快了本国煤层气的开发利用。近年来,我国开始重视煤层气的开发利用,2009年7月,港华燃气与山西晋城无烟煤矿业公司建成了我国第一个上规模的也是目前地面抽采瓦斯规模最大的煤层气液化项目。
因煤层气中含氧量低,目前,我国地面抽采的高浓度瓦斯利用技术相对比较成熟。但井下抽采的低浓度含氧煤层气,一直没有得到很好解决,一个关键的制约因素就是低浓度煤层气中的氧气是危险的助燃剂,在煤层气的利用上存在较大风险。
2008年9月至今,煤炭科学研究总院重庆研究院与中国科学院理化技术研究所合作,研究形成了一套完整的煤矿区低浓度煤层气含氧液化工艺技术方法,研发出4800m3/d低浓度煤层气含氧液化试验装置,在重庆松藻煤电有限责任公司逢春煤矿建立了中试基地。通过本项目的研究,创新性地提出并形成了一套以湿法脱碳、分子筛脱水,以混合冷剂制冷、在低温低压下同时液化与分离含氧煤层气中的CH4、O2和N2的技术方法,研制出了4800m3/d低浓度煤层气含氧液化中试装置和含氧煤层气液化冷箱等关键设备。
据中科院理化技术研究所高级工程师张武介绍,目前国内煤层气液化普遍采用的是先脱氧、后液化的“催化脱氧”技术,该技术存在工艺比较复杂、能耗高、投资大等不足,并且对煤层气的甲[FS:PAGE]烷含量要求也比较高。“这次和重庆研究院共同建设的深冷液化装置,克服了上述弱点,同时具有四项国家专利技术,成果达到国际领先水平。4月12日,项目通过了以中国煤炭科工集团西安研究院张泓教授为组长的国务院重大专项项目专家办组织的验收。”张武告诉记者。
“低浓度煤层气深冷液化工业试验装置和以前利用的技术生产工艺不同,以前的技术对煤层气浓度要求高,必须达到60%-70%,现在30%以下的就可以。这套装置的建成,让我们看到了低浓度瓦斯的利用前景,这个技术如果真能大力推广应用,不仅松藻煤电的瓦斯开发利用能再上一个台阶,对我国其它煤矿的瓦斯利用也有示范作用。”逢春煤矿党委工作部副部长张登泽说。
多项技术保证安全生产的
据王长元介绍,低浓度煤层气含氧液化工艺是先将气体混合物冷凝为液体,然后再按各组分蒸发温度的不同,在精馏塔内将它们分离。其工艺与目前采用的先除氧再液化或者先采用变压吸附浓缩再液化的工艺相比,具有液化甲烷纯度高、回收率高、成本低、占地面积小的突出优点,与目前已有的分子筛脱碳脱水以及膨胀机制冷的含氧液化工艺相比,具有工艺流程更合理、能耗低、运行成本低的优点,能够为工业化大型含氧液化装置放大设计提供参考。
低浓度煤层气分离提纯过程中甲烷爆炸性问题是制约煤层气利用的技术瓶颈,本项目通过有效的控制煤层气通道的压力与温度、系统泄压保护、防雷防静电、分散控制系统(DCS)及紧急停车系统(ESD/SIS)等安保措施来解决低浓度含氧煤层气在压缩、净化、液化与分离过程中的安全问题。
根据工艺的要求,全厂所有的工艺装置均采用分散控制系统(DCS)进行数据采集和过程控制。紧急停车系统及关键设备联锁保护都设置必要的自动联锁保护系统(ESD/SIS)。通过DCS/SIS系统的设置,保障了装置的可靠运行和安全运行。
大规模应用尚需时日
“评价一项技术的好坏,能否应用于实际是非常重要的一点。甲烷气体被液化后,体积将缩小为原来的1/625,运输成本比压缩气体低,与管道输送相比,液化运输更为灵活和方便。同样体积的LNG与液化天然气相比,燃烧时间要多出好几倍。在目前能源紧缺的情况下,将低浓度含氧煤层气采取直接液化分离的方法加以利用,可以起到很好的示范作用并加以推广应用,不仅可以充分利用能源,减少环境污染,而且对煤矿企业也能产生较好的经济效益。”王长元告诉《中国能源报》记者。
同时,他也并不否认目前存在的困难:“目前只是通过试验获取技术参数,还未实现工业化。我们在中试基地还需进行大量的试验研究,为工业化装备提供设计依据。”
“虽然我们的技术已经达到了国际先进水平,但离大规模应用还有一定距离。一加一不一定等于二。从小装置到大装置,工艺参数会发生很大变化,对设备的安全性等要求也更高。想要达到工业化生产的规模还要解决很多技术问题。”王长元说。( 责任编辑:管理员 ) |
|
|
|
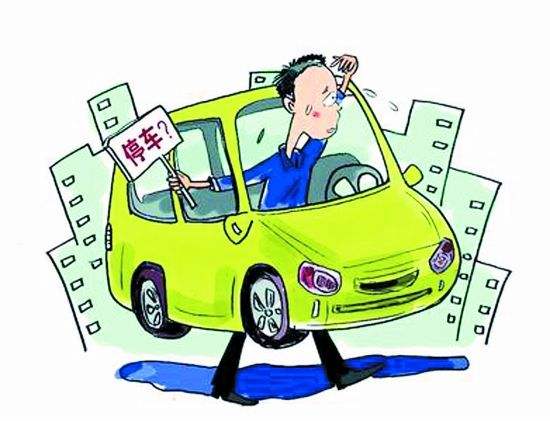 |
|
因地施策,破解停车难 |
|
|
|
|
|