 |
您目前的位置:首页--企业黄页 |
|
“现在我们正在进行平衡25万吨/年合成氨、35万吨/年尿素的技改工作,总投资1.2亿元左右,建设十几个工程项目。”前不久,记者来到晋煤冀州银海化肥有限责任公司采访,公司副总王峰森指着厂区西侧正在建设的工地向记者介绍说,技改完成后,该公司全部生产设备将实现全系统的最佳匹配和经济运行,工艺和设备潜力将充分发挥,实现节能降耗和经济效益的最大化。
银海公司是河北省循环经济试点企业,近年来该公司紧紧围绕循环经济、节能减排、清洁生产三大主题,明晰技术创新和节能降耗路线,各项消耗指标在全国同行业名列前茅。
“减量化、资源化、再利用”,银海按照循环经济发展理念更新设计生产工艺,实现了副产品全利用、零排放。仅围绕一个“水”字,银海就做足了文章。他们申请中央环保专项资金600万元,自筹资金1800多万元,实施了污水零排放综合整治工程;投资300多万元实施了废水终端处理项目,对全厂废水进行全部处理,大部分回用,少量达标排放。
此外他们还投资数百万元进行了脱硫工艺改造、含氨废水提浓、原料气醇烃化精制等技改项目项目,完成了外排物中各类物质的分类处理,尽最大限度回收再利用。“通过这些项目的实施,银海污染物不但完全达标排放,外排量还大大降低。通过节煤、造气废水零排放和废水综合治理,我们每年可增加效益2000多万元,削减COD1100多吨、二氧化硫1300多吨。”说起公司节能减排的成效,董事长、总经理聂平海不无自豪,“其实这些都得益于公司这些年持续不断的技改。”近8年来,银海共投入资金3.5亿元,实现了生产系统从头至尾的彻底改造,生产装备和生产工艺得到了极大改进。
把正在进行的对标工作与节能减排有机结合起来,这是银海实现节能降耗的另一个心得。他们盯住行业高端,组建创新团队,引进高层次人才,加大技术改造力度,把对标工作与节能减排结合进行。目前银海合成氨耗白煤由过去的1.54吨降到现在的1.25吨、合成氨耗烟煤由过去的180千克降到现在的25千克、合成氨耗电由过去的1740千瓦时降到了现在的1300千瓦时。
“我们的这些指标在全国同行业内都是领先的。”王峰森介绍说。近年银海仅引用中国氮肥协会推荐的节能减排新技术就达20余项,使“两煤一电”消耗大幅度降低。此外银海还通过合同能源管理方式,引进了青岛华捷透平动力有限公司生产的汽拖动,使三废锅炉生产的中压蒸汽能够充分利用,此举每天节电近3.3万千瓦时,年节约资金440万元。(作者:赵引德、杨万宁)( 责任编辑:管理员 ) |
|
|
|
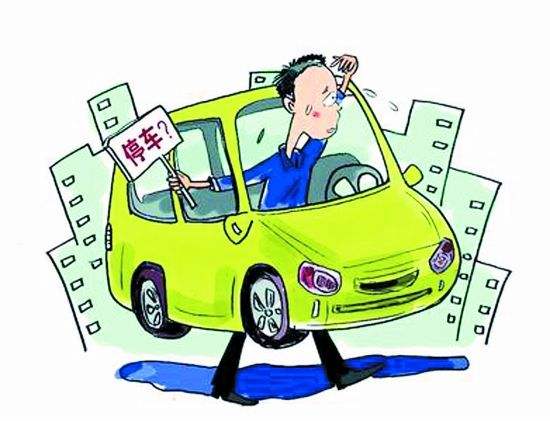 |
|
因地施策,破解停车难 |
|
|
|
|
|